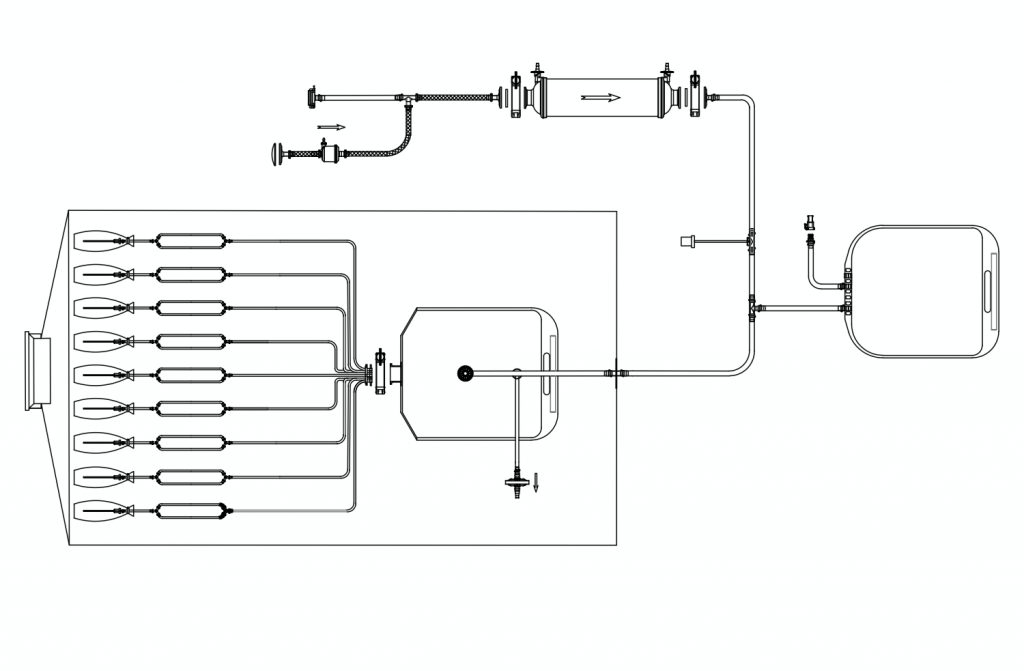
MDI Single Use filling lines are customized to suit new as well as existing fill and finish systems. These are designed to comply with regulatory requirements such as “Final sterile filtration should be carried out as close as possible to the filling point” and “The integrity of the sterilized filter should be verified before use and should be confirmed immediately after use by an appropriate method such as a bubble point, diffusive flow or pressure hold test” (European Union Current Good Manufacturing Practices).
MDI disposable single-use final fill assemblies ensure:
- Quick turnaround time
- Product and operator safety
- Reduced risk of cross-contamination
- No cleaning validation
- Increased flexibility and productivity
Disposable Filling Lines for Isolator/RABS
These ready-to-use gamma sterilized filling lines are also available housed within a specially designed bag with a Beta Port for transfer into and out of an Isolator or RABS.
These assemblies are pre-validated, pre-assembled, pre-sterilized systems with bags, tubings, connectors, filters, and filling needles, placed inside a beta port bag for easy and secure insertion and removal around the aseptic filling system.
The beta port bags come with a special port which connects the sterilizing filters with the filling lines, making it convenient for the user to conduct PUPSIT (Pre-Use Post Sterilization Integrity Testing)
Continue reading “Single Use Final Fill Systems to meet stringent regulatory requirements”